Showerhead Reactors: Overview
Showerhead reactors employ a perforated or porous planar surface to dispense reactant gases more-or-less uniformly over a second parallel planar surface. Such a configuration can be used for batch processing of multiple substrates, but also lends itself to processing of single round wafers. A showerhead reactor might look something like this:
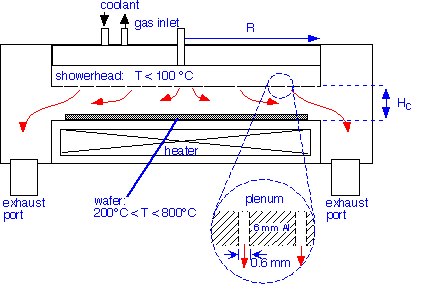
Wafers can be heated separately from the gas dispense and chamber wall, so showerhead reactors are generally cold-wall: only the surface holding the substrate need be at the process temperature. This fact is often helpful in minimizing deposition on chamber walls. Coolant may be provided to help in controlling the temperature of the showerhead (to prevent deposition reactions taking place within it and clogging up the pores in the showerhead). Many deposition processes employ precursors which can exist as liquids at room temperature (TEOS and related organosilanes and siloxanes, TDEAT and TDMAT, most copper precursors, WF6, etc.). When working with such materials it is often useful to warm the walls of the chamber above ambient temperature to avoid any possibility that the precursors may condense on the walls or inside the showerhead plenum.
Showerhead reactors lend themselves to implementation of plasma-enhanced processes, in which connection they are also referred to as parallel-plate. In most PECVD reactors the top and bottom electrodes are about the same size. Note that if one wishes to ground the wafer electrode, which is often convenient for safety and wafer loading, the showerhead has RF power applied: it is then necessary to incorporate appropriate insulating sections in the gas supply system, to avoid creating a parasitic discharge in the gas feed lines to the chamber.
The diameter of a showerhead reactor is determined by the size of the wafer or substrate batch to be processed; in particular, single-wafer reactors usually employ a bottom electrode similar in size to the wafer. A very important chamber design parameter is the ceiling height or electrode gap, which we here denote as Hc. Changing this height has several important effects: the chamber volume and thus the surface-to-volume ratio is modified, affecting the residence time, consumption time, and radial velocities. Changes in the residence time strongly influence the extent of gas phase reactions. The individual gas streams exiting from the perforations in the showerhead need to merge into a smooth flow field to give good local film uniformity, a process assisted by larger values of Hc. A showerhead configuration operated as shown (hot surface below a cooled surface) always has the potential for natural convection of the Benard variety if operated at high pressures (hundreds of Torr), and such a tendency is strongly influenced by the height through the Rayleigh number. When operated as a plasma reactor, changes in Hc can have important effects on the plasma density and potential. Finally, changing Hc is often important in controlling the radial uniformity of the deposited film thickness. For all these reasons it is useful to be able to change Hc easily during process development, either through simple hardware changes or by providing adjustable mounting of the substrate electrode.
The hole configuration of the showerhead is often important in determining uniformity of deposition. It is therefore useful to design the showerhead so that the perforated faceplate is easily removed and another of possibly different design substituted. Changes in the plenum, such as the addition of blocking plates or changes in the gas inlet configuration, can also be used to improve uniformity. Operation at high pressures (greater than a few Torr) requires that the holes be small, as otherwise a localized hollow cathode discharge may occur in the holes, causing heating and erosion. [Hollow cathode discharges are the result of thermionically emitted electrons being trapped within an equipotential "hole" when the sheath thickness becomes smaller than the hole diameter; the trapped electrons bounce around and can do a lot of ionization, just as in the case of a magnetically confined discharge.]
Variations on the basic showerhead include the provision of multiple gas plenums arranged in e.g. circumferential rings, so that multiple gases can be dispensed without mixing in the plenum: such capability is useful in deposition of TiN, where precursor chemicals such as TDMAT or TDEAT react rapidly with ammonia even at room temperature and low pressures. Reactors have also been built with field-configurable showerheads, implemented by drilling large numbers of threaded holes at regular intervals; the user then has the option of filling a hole with either a perforated bolt or a screw with an o-ring seal, varying the pattern of gas dispensation. Such configurable arrangements are limited in the hole density that can be employed due to the difficulty of handling very small parts and the practical limit in how many adjustments can be made by hand; therefore, as we will discuss, they can only be used for conditions of relatively low molar flow (large diffusion length) where the widely-separated entering gas streams merge in the available gap spacing Hc.
In practical reactors, it is always necessary to be able to access the chamber area for cleaning and maintenance. Most showerhead reactors are configured with a lift or hinge, so that the showerhead may be lifted away from the process area. Provision of gases to the movable showerhead can be done with flexible tubing, but plastic tubing is typically porous and a source of contaminants; stainless steel bellows is expensive and can be a particle source. A common trick is to provide gases through the bottom half of the chamber to one or more holes in the faceplate where the top and bottom seal together: a small o-ring mounted around the holes allows a corresponding hole in the top plate to form a sealed passage for gas supplies when the chamber is assembled, without impeding disassembly. The consequent "dead space" between the sealing faces within the o-ring formed when the chamber is reassembled must be carefully purged before processing if moisture-sensitive processes are to be performed.
Return to Tutorial Table of Contents
Book version of the CVD Tutorial