Tube Reactor Overview
Horizontal and vertical tube furnaces are widely used in semiconductor processing due to their simplicity and productivity: round wafers can be stacked in a slotted quartz boat and processed in batches of up to 100-200 wafers at a time. CVD reactors are elaborations of the basic furnace design originally used for oxidation and annealing.
A tube CVD reactor is shown schematically below. The tube is typically fabricated of quartz, and of large enough diameter to load the wafer size desired with some margin. The tube is inserted in a resistively heated box. The box typically has 2 or more independently controlled heating zones to allow some control of axial temperature along the reactor. The reactor shown is in a horizontal configuration, but vertical reactors have become more popular in recent years due to greater simplicity in automated loading, smaller footprint, and lower particle counts. (The operating principles are identical, since as we'll see temperature gradients are small in these reactors and natural convection plays no role in LPCVD conditions.)
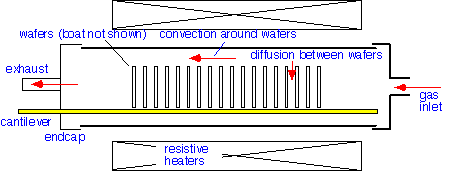
Wafers are typically stacked vertically in slots in a quartz boat. The spacing between wafers is minimized to increase the number of wafers that can be loaded, but as we'll discuss, transport between wafers imposes limitations on how close the spacing can be. In a horizontal configuration, the boat can rest on the surface of the tube, but more modern reactors suspend the boat on a cantilever (a rod held at one end) to avoid scraping and particle formation. Gas is dispensed at one end and exhausted at the other (though more elaborate arrangements are often employed). The endcaps seal the tube. Operation at low pressures (LPCVD) generally requires polymeric seals (o-rings) on the endcaps, which may then be water-cooled to protect the o-rings from the high process temperatures, and vacuum pumping systems which are tolerant of dust accumulation.
These reactors typically have a "flat zone" in which the axial temperature is very nearly constant. The flat zone temperature can be controlled to within better than one degree C. The size of the flat zone determines the number of wafers than can be loaded in a single run.
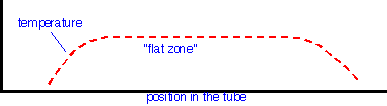
Tube furnaces are hot wall reactors: everything is at the same temperature, and in general the film being deposited ends up on every exposed surface of the tube. The tube and wafer holding hardware must be cleaned periodically to avoid spalling and particle formation. Cleaning can be performed by removing the tube and quartzware and immersing them in appropriate wet chemical baths, although this procedure is complex, relatively dirty, time-consuming, and expensive, since large quantities of toxic acids must be handled. In situ cleaning using thermal decomposition of NF3 has been reported as an alternative procedure for polysilicon or silicon nitride systems. NF3 is reasonably safe at room temperature but readily decomposes to release fluorine at 500 °C and above. Careful temperature control is necessary to prevent thermal runaway due to the heat generated by the decomposition.
Reference: "A simple in situ cleaning method for LPCVD polysilicon and silicon nitride tubes" B. Huling, G. Engle, C. Schneider, R.J. Gibson and R. Ridgeway, Solid State Technology October 1994 p. 73.
Return to Tutorial Table of Contents
Book version of the CVD Tutorial